Decarbonising heat in manufacturing: five practical considerations
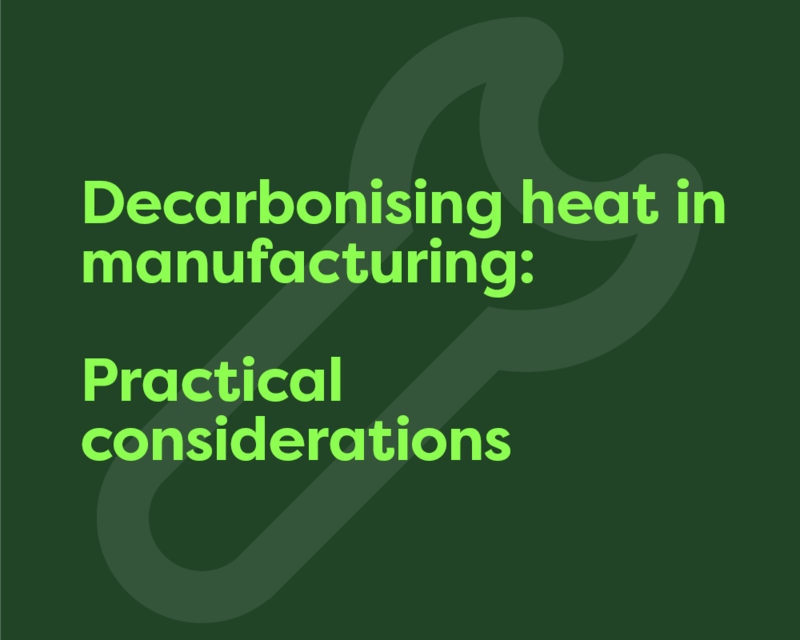
Now that the first science-based global standard for corporate net zero targets has been published, there is more clarity for businesses aiming to achieve Net Zero. For most group and site managers concerned about operational emissions this is likely to translate to a 90% reduction in scope 1 and 2 emissions!
Although the renewable electricity technology and renewable electricity markets are quite mature, many companies are concerned with the means of practically decarbonising heat.
We have been helping many manufacturing clients to develop and execute strategies for Net Zero and I would like to share with you some practical considerations from our direct experience.
1. Understand the quality of heat you need to supply to your operations.
When considering decarbonisation, think “how hot?” not “how much?” heat you require to supply to your processes:
- This will help you to identify areas of the site which can be met with alternative sources of heat other than steam or direct gas fired heaters.
- This could be the start of decoupling some heat users from aged steam or gas mains infrastructure. We have found that many business can significantly reduce the reliance on gas-fired steam generation, arguably with commercial benefits.
- It is also important to future proof the design of any new (or retrofit) heat sinks by enabling these parts of the plant to be fed by a range of heat sources for when emerging technologies (e.g. high temperature heat pumps) become commercially viable.
2. Work out your overall heat system efficiency and economics.
With recent increases in commodity prices, most businesses are re-evaluating the cost-effectiveness of existing heat generating plants. Although the price differential between gas and electricity is likely to remain significant, the marginal capital and operational cost of decarbonising existing low-efficiency steam heating plants could be lower than initially thought.
In our experience, centralised steam generation plants can exhibit efficiencies as low as 50-60% when comparing primary fuel input to actual heating demand, making electrification a viable option.
3. Plan early for the future of your co-generation plants.
Gas-fired CHPs are still very much a key tool in reducing utility costs across many manufacturing sectors. Businesses are currently considering their options between a lower-utility cost base (with co-generation) and a lower-carbon heat generation base (without co-generation); however incentives and/or levies may alter this dilemma in the future.
Reducing the reliance on gas CHP is looking more positive for those assets that have sub-optimal usage of low temperature hot water or are de-rated and/or are closer to their end of life. Alternatively, where green gas is available, this may be ideal for extending the life or modifying existing CHP assets.
Hydrogen-powered cogeneration plants are currently drawing lots of interest. The UK is currently pursuing a 'twin track' approach of blue hydrogen (i.e from fossil fuels with carbon capture and storage) and green hydrogen from renewables. How fast these options become available at scale will depend much on government subsidisation. Under any scenario however, a cheap and plentiful supply of low carbon hydrogen looks a long way off. We would expect hydrogen to be used in high temperature applications and other hard-to-abate sectors like steel and heavy transport in the first instance.
A world where green hydrogen is commercially viable as a heat source is likely to be a world where there is relatively ready access to low cost electricity. It is likely in this instance that using hydrogen to generate heat and then using renewable electricity will make the most sense.
4. Explore local, low carbon sources of heat.
Councils are being encouraged to find alternative ways to decarbonise and the UK government is providing decarbonisation funding. Already, low carbon district heating schemes (see examples here and here) are being developed in some cities and businesses in these locations could look to take advantage of the schemes – in some cases without significantly upsetting their current heating infrastructure.
Alternatively, local developments for green gas, biomass, biomethane or hydrogen may offer a potential solution; these often come with questions around their green credentials (e.g. sustainable supply of biomass) commercial considerations (e.g. cost per kWh delivered) and technical considerations (e.g. modification of burners for alternative fuels). The above opportunities are likely to be strongly dictated by locality.
5. Assess the risk of relying on renewable guarantees of origin.
As for electricity, there is now a market for Renewable Gas Guarantees of Origin (RGGOs) which can potentially provide businesses with a fallback position and there are now schemes across Europe which could provide a benefit for operations spanning several countries.
However, it is unlikely that this market can grow fast enough compared to the demand for certificates from heat-hungry industries and should only be looked at as a last resort. In simple terms, there is not enough biogas for everyone and the competition is likely to be very high.
We need further collaboration to overcome this challenge.
There is significant amount of research going on particularly around meeting high-temperature heat demand. Verco are developing collaborative projects to overcome the challenges around decarbonising heat, particularly looking at the application of heat pumps for industrial processes.
If you want to learn more about this, here are some useful resources:
Podcast: The challenges of decarbonising heat in manufacturing
Webinar: Decarbonising heat in manufacturing
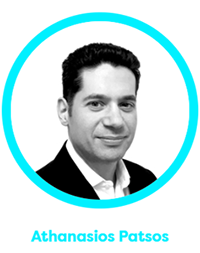